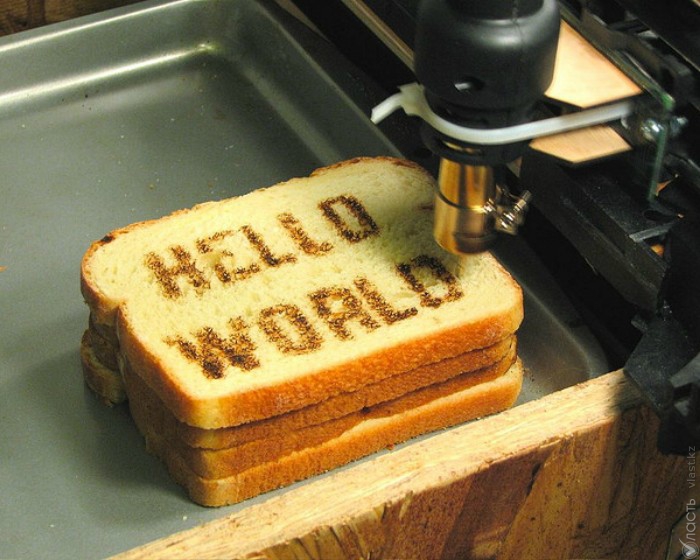
Кристин Мэйчер
3D печать или — как ее иногда называют — «технология послойной печати» дает возможность создавать физические объекты послойно из метала, термопластика и даже керамики на основе заданного дизайна.
Данную технологию уже применяли в создании определенных специфических продуктов — сложных для производства традиционным путем — таких, как слуховые аппараты и части двигателей самолетов.
Технология 3D печати уже широко применяется несколькими компаниями. Например, один из мировых лидеров в разработке инновационных медицинских технологий «Align Technology» использует ее для производства зубных брекетов «Invisalign», разработанных под индивидуальные особенности пациентов. А в аэрокосмической промышленности технология послойной печати применяется для создания высокотехнологичных приборов. Крупнейший мировой производитель «General Electric» разработал топливную форсунку, напечатанную на 3D принтере, с использованием сплава кобальта, хрома и молибдена. Деталь входит в наш список Лучших технологий 2013 года. И по словам представителей компании в ней меньшее количество частей, и она на 25% легче и в пять раз долговечнее, чем предыдущие форсунки.
Да, первопроходцы есть. Но тем не менее привлекательность данной технологии ограничивается высокой себестоимостью и низкой скоростью. Чтобы технология 3D печати получила более широкое распространение, весь процесс должен стать дешевле, а дизайн принтеров нужно изменить так, чтобы они стали быстрее и поддерживали использование более широкого спектра материалов.
«Этот рынок еще слишком затратный», — объясняет Доминик РиТцель, специалист в сфере технологий послойной печати Центра исследований и инноваций группы компаний «BMW», расположенного в Мюнхене. Хотя 3D печать помогает сэкономить на использовании материала, необходимого для производства какой-либо части, сама подготовка и разработка материалов для печатных машин может быть затратной. И результаты не всегда удовлетворительны. В конечном итоге традиционный способ формового литья остается более экономичным для массового производства, заключает Ритцель.
Компания «BMW», вложившая значительные инвестиции в 3D печать на основе метала и пластика с момента покупки своего первого устройства послойной печати в 1989, применяет технологию для быстрого прототипирования и оценки потенциала новых дизайнов автомобилей , но не для массового производство частей. Согласно заявлению автопроизводителя, выпустившего 2 миллиона машин в прошлом году, стоимость печатных устройств и материалов нужно будет значительно сократить, чтобы компания могла рассмотреть вопрос массового запуска.
Одни исследователи работают над возможностью снижения затрат на изменение формы метала и пластика для 3D принтера. Другие надеются найти способ исключить необходимость изменения формы.
Компания «Metalysis», базирующаяся в Ротерхэме (Великобритания), заявила, что разработала способ значительного сокращения стоимости 3D печати посредством использования титана, который ценится за свой легкий вес и высокую прочность.
В отличие от традиционного производства, в котором титан можно использовать в его натуральном состоянии, для применения технологии послойной печати требуется превратить метал в порошок. Этот процесс довольно затратный. Используя метод, основанный на исследованиях специалистов из Кембриджского университета, компания «Metalysis» смогла создать титановый порошок при затратах на 25% ниже, чем при обычном процессе.
Национальная лаборатория «Oak Ridge» при Министерстве энергетики США (Теннесси) работает над разработкой устройства, которое могло бы печатать с использованием высококачественного пластика, который широко применяется в традиционном производстве. Портативный принтер, который возможно будет запущен в коммерческое производство уже в 2015 году, при печати использует термопластичные пластины, армированные стеклянным и углеродным волокнами. Стоимость этих пластин, широко применяемых в литейной индустрии, варьируется между $1 и $10 за пол килограмма. Также принтер, разработанный «Oak Ridge», может использовать их для производства широкого спектра объектов, начиная доступным по цене оборудованием и заканчивая беспилотниками. Более того — как уточняет сотрудник лаборатории Лонни Лав — есть дополнительное преимущество: тесты показали, что соединение материалов в процессе послойного производства увеличивает их прочность и плотность благодаря соединению углеродных волокон.
Помимо стоимости еще одна проблема заключается в возможности применения 3D печати в массовом производстве. Существующие системы могут производить продукцию по 15 кубических сантиметров в час. Это означает, что на изготовление предмета размером с обувную коробку, потребуется несколько дней или даже недель. Но новое устройство, разработанное компанией «Oak Ridge», может печатать в 200 или даже 500 раз быстрее. Обратная сторона — страдает качество отделки поверхности. И для придания окончательного внешнего вида изготовленным частям все равно приходится проходить через стандартный процесс обработки.
Проект Google «Ara», в рамках которого планируется печатать сборные части для сотовых телефонов к 2015 году, также набирает обороты. Поставщик компании «3D Systems» — первый производитель коммерческого 3D принтера, пересмотрел свой первоначальный подход. Новый процесс печати включает в себя сборную линию, на которой части двигаются на специальной ленте и отливаются посредством закрепленных сверху печатающих головок. «3D Systems» утверждает, что их технология уже побила рекорд скорости формовой заливки.
Помимо скорости и стоимости производители столкнулись с еще одной проблемой — совершенствованием состава материалов для придания им прочности и универсальности, необходимой для промышленного применения. Лаборатория реактивных двигателей NASA в Пасадене (Калифорния, США) в сотрудничестве с Калифорнийским институтом технологий и Государственным университетом Пенсильвании использует лазеры для расплавления металлического порошка и создания сплавов, которые затем слоями выкладываются вокруг вращающегося стержня. Процесс может дать производителям возможность использовать два разных сплава во время производства и изготавливать части из более чем одного вида метала.
«Мы больше узнаем о том, как взаимодействуют вместе устройства и материалы, как они создают не только форму, но и определенные свойства», — говорит Кристина Фурстос (Christine Furstoss), технический директор департамента производства и материалов компании «General Electric».
«Придание объекту свойств в процессе создания его формы — это то, к чему десятилетиями пытались прийти в индустрии ковки и литья», — добавляет Фурстос. «Мы же пытаемся прийти к этому за несколько лет».
Technology Review, The New York Times
Перевод для Vласти — Нины Кузнецовой